Timber remains a $40 billion industry in the Pacific Northwest, with logging trucks and mills regular sights across Oregon and Washington. And like many industries, timber is adopting new technologies to improve efficiency, safety and productivity. KLCC’s Brian Bull explores the latest “cutting edge” tech.
Retired logger Jack Abernathy is being reckless. He’s riding on the hood of a semi loaded with trees, barreling down a rugged, wintry slope.
“Oh man, now I’m going down the road! Woo woo woo! Wow, that’s fantastic! Wheeee!”
Okay, technically he is…and isn’t. Abernathy is seeing this all through a pair of virtual reality goggles. He’s seated safely at the Papè booth at the 79th annual Oregon Logging Conference in Eugene.
Technician Christine Cantamessa checks in.
"What do you see, Jack?" she asks him.
"I see a guy cuttin’ down a tree!" he yells.
"Alright!"
"That was neat. A guy’s in front of me with a log loader…”
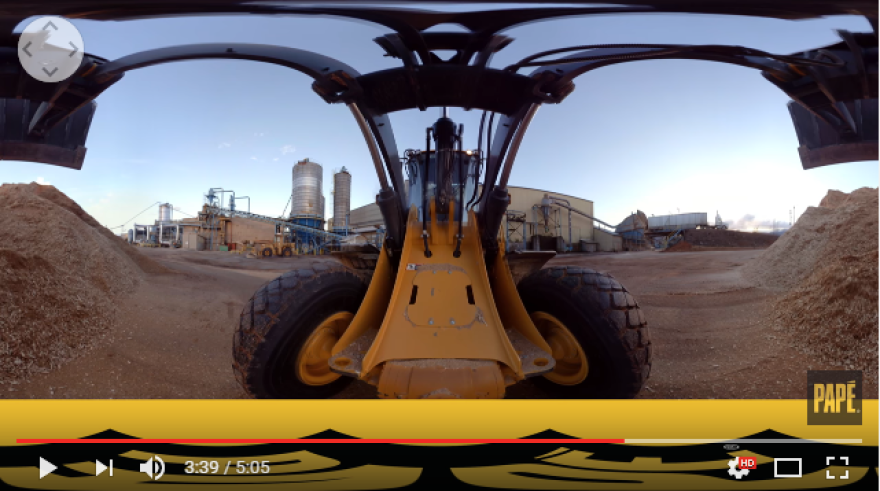
It’s reactions like these that please Owen Garrity. He owns FPW Media, which produced the 360 Papè virtual reality experience.
He says cameras were set up in spots too dangerous for people.
“Usually it’s 200 or 300 feet while the camera and where you really feel you are, is maybe 3 feet away," says Garrity.
"We filmed in multiple different locations: Timber Products Mill in Medford, and White City. As well as two different logging sites…”
The virtual reality experience at the logging conference draws steady crowds, who may have never set foot on a logging site or mill, otherwise.
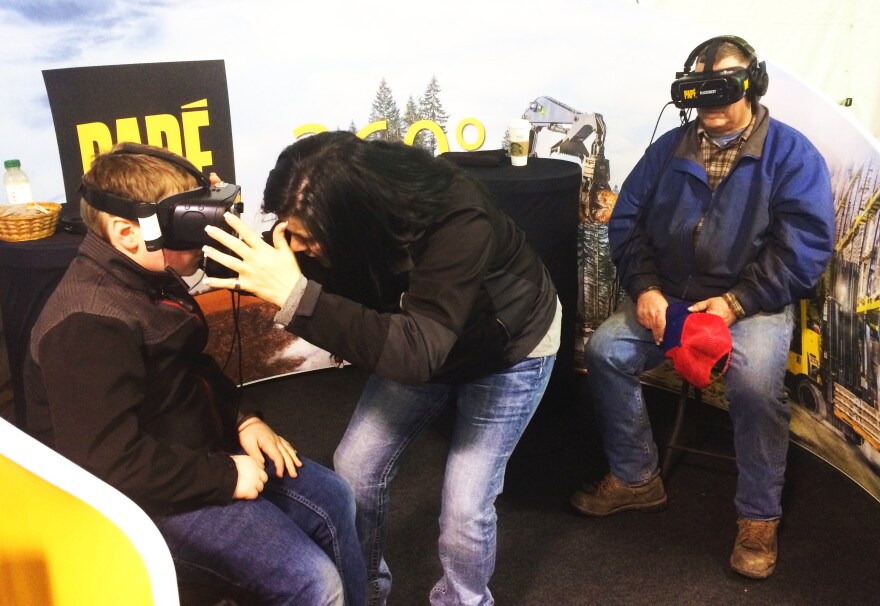
As to whether this tech best enthralls, educates, or entices potential timber employees, Jeff Wimer says…
“Honestly, I think it serves all three. I do think it is good entertainment value, but as far as recruitment goes, it’s really good because a lot of people don’t realize that we are more modern technology.”
Wimer manages the student logging program at OSU’s Department of Forest Engineering. This includes a harvest simulator…a chair, console, and monitor set-up that costs roughly $70,000.
“Running one of these big machines, is a lot like a video game anymore.”
One that puts you into the operator’s chair, downing trees versus space invaders.
“What it will do, is allow a person to drive through a forest on 8 wheels, and harvest the trees right on the hill slope. Then the next person can come through with what we call a forwarder that can load them into bunks and then bring those to roadside to be loaded onto a truck.”
Wimer says it’s actually more expensive – and dangerous --in the long run to bring students into a real machine.
“It’s very realistic," he says, nodding at the monitor. "The only complaint I have is the depth of field, the 3-D feel, is not very accurate.
"But man, you can cut a lot of trees.”
After 10 hours have been successfully completed in the simulator, students can then strap themselves into the real deal…sawdust and all.
And timber’s integration of new technology isn’t just screens and simulations. There’s also unmanned aerial systems, or drones.
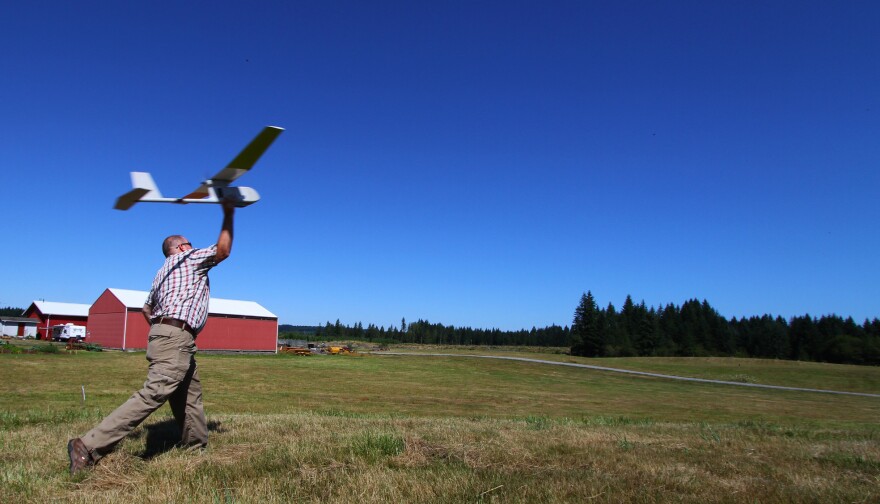
“In the timber industry, we have a lot of acreage, they’ll also use more of a fixed-wing or flying wing, besides just the multi-copter design…” says Lane Community College flight instructor Sean Parrish.
He navigates a small drone around a conference room. He says these maneuverable craft can do tasks faster, safer, and more often than people.
“Monitoring the timber…especially in the first few years of its growth. Spraying for pests and disease, things like that will also be something that will come into play," Parrish tells KLCC.
"But the big one I think would be the monitoring of the crop with multispectral imagery, and then taking that back to analysts that can see what applications that they need to apply to get a better harvest.”
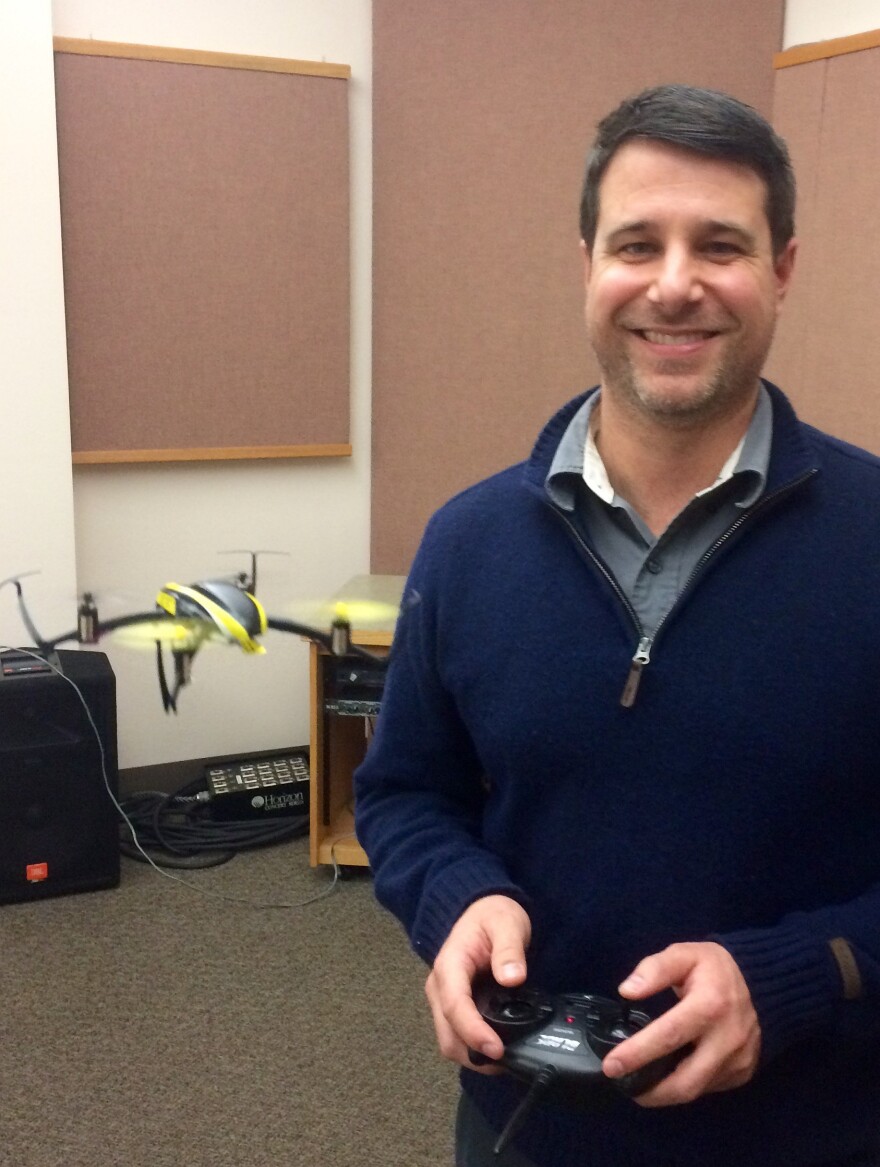
“It’s a lot more than just guys with axes, it’s pretty high-tech anymore,” smiles Milt Moran of Cascade Timber Consulting in Sweet Home. He says there’s innovations going on with steep slope logging…where a tandem set of machines use a tethering system and remote control to do tree-cutting.
And on the materials and engineering side, there’s buzz on cross-laminated timber…multi-layered panels that Moran says is stronger and safer than concrete or steel.
“The World Trade Center…when those collapsed, it was because the steel had failed because of the extreme heat," says Moran.
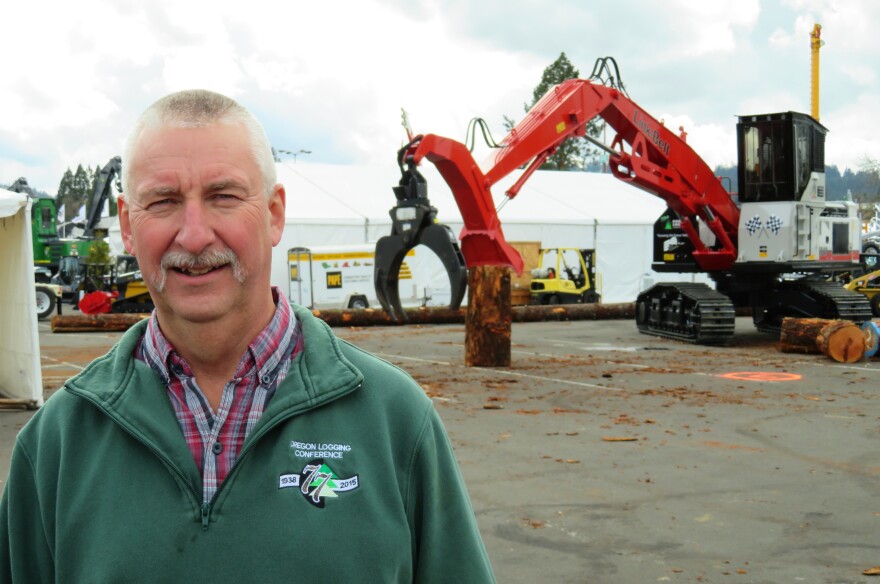
"And what we’re looking at with large wood timbers, is that they actually char over, they found that they are protecting the steel joints with the bolts and the steel is, with thick wood members.”
On the safety side, GPS is being explored as a way to monitor the location of timber workers out in the woods. This can ensure a logger is out of harms way when trees come down, or can help find those who are lost.
Back at the Papè virtual reality exhibit, a long line of kids wait their turn to slip on the goggles. For some of these youngsters, it’s a glimpse at their possible future.
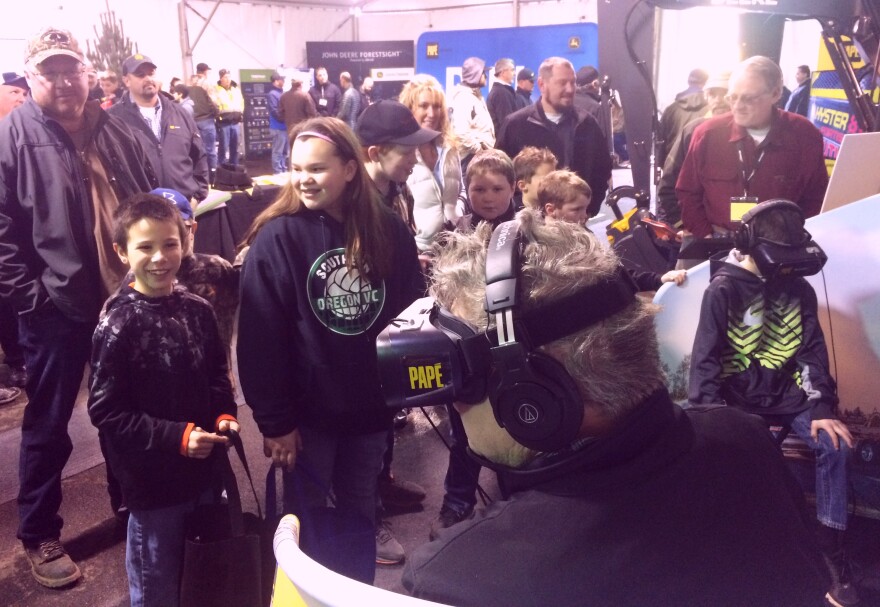
For retired logger Jack Abernathy, it’s a good dose of nostalgia.
“I used to set chokers out in the woods. It’s a thing that goes around the logs, and you hook it into a bell," he recalls.
"It was pretty nice to revisit that experience," I tell him.
"Yeah, yeah, yeah…"
"Well, it’s a pretty big crowd, would you recommend this to other people?” I ask.
"Yes, I do, yes I do! Really truly.”
And so I take my turn. Christine Cantamessa walks me through it.
“And where are you?” she asks.
"I’m on a…a road," I answer, turning my head back and forth.
“I think you’re on a truck!”
"I think I am," I confirm, as Cantamessa laughs.
For all the technological innovation though, some in the timber industry say the real leap will be to fill a shortage of workers. That’ll require some old-fashioned outreach.
Copyright 2017, KLCC.